カーボンフットプリント(CFP)は、製品のライフサイクル全体にわたる温室効果ガス排出量を算定し、環境負荷を「見える化」する手法です。特に欧州電池規則では、CFPの開示が電池メーカーに義務付けられ、将来的には排出量の上限値が設定される見込みです。本記事では、CFPの基本概念から算定手法、国際規格との関係、欧州規制の動向、企業が求められる対応策まで詳しく解説します。
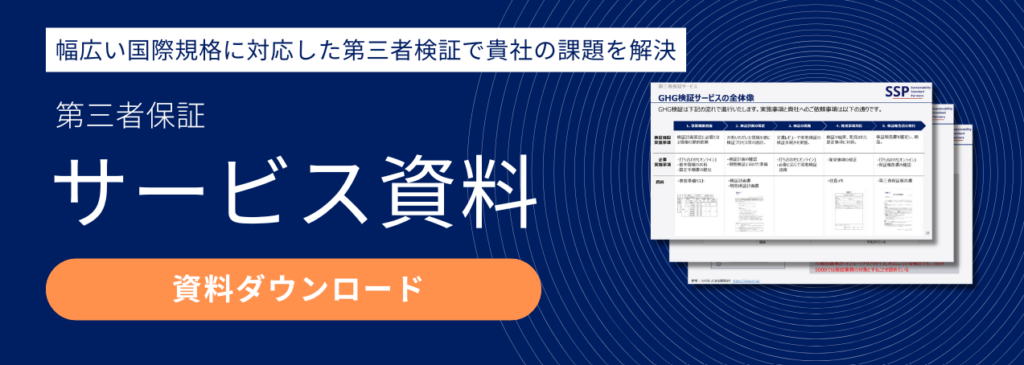
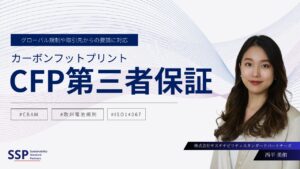
1. カーボンフットプリント(CFP)とは?
カーボンフットプリント(Carbon Footprint of Product)は、製品のライフサイクル全体を通じて排出される温室効果ガスの総排出量を指します。
CFP概要
具体的には、原材料の採掘・精製から部品生産、電池セル製造、組み立て、物流、使用後の廃棄・リサイクルに至るまでの各プロセスで発生するCO₂などの温室効果ガス排出量を算定し、CO₂換算で合計したものです。CFP算定では一般にライフサイクルアセスメント(LCA)と呼ばれる手法が用いられ、ISO 14040/44など国際規格に準拠して評価が行われます。
電池のCFP
特にエネルギー集約型の製造プロセス(電極材料の焼成や真空乾燥、セル組立時の恒温恒湿管理など)や、原材料(金属資源)の採掘・精錬時の排出がCFPに大きく影響します。
例えば、ニッケルやコバルトの採掘・精製は膨大なエネルギーを要するため、それらを多く含む電池はCFPが高くなる傾向があります。欧州電池規則では、このCFPの算定と開示が電池メーカーに対し初めて法的義務として課されました。
これにより、各社は自社の電池製品が「どれだけのCO₂を排出して作られたか」を明確に示す必要があります。CFPは一種の環境性能指標であり、これを企業間で比較できる形で公表させることで、より低炭素な製品づくりへの競争を促す狙いがあります。CFP算定にあたっては、いくつかの重要な定義・範囲決めがあります。欧州電池規則では、使用段階の排出はCFP算定に含めないことが認められています。
これは、電池の使用時(例えばEVを走行させる際)に排出されるCO₂は主に発電所由来であり、電池製造者の管理範囲外であるためです。一方で、電池が廃棄またはリサイクルされる際の処理工程については、製造者が設計段階でその容易さに影響を与えられることから、CFPに含める方向で議論されています。基本的には原材料調達から工場出荷、廃棄・リサイクルまでの範囲(いわゆる「Cradle to Grave」ただしUse段階除く)がCFP評価の対象となります。
CFPの単位は「kg-CO₂e(CO₂換算キログラム)」で表され、電池1単位あたり(例えば1kWh分のセル、または一個の電池モジュールなど)の数値として報告されることになります。値が小さいほど環境負荷が小さい「低炭素な電池」ということになります。
2. 欧州電池規則におけるCFPの位置づけ
欧州電池規則では、CFPは電池の環境性能を評価する中核的な指標として位置づけられています。規則本文では第7条にCFPに関する規定が置かれ、以下のような段階的措置が講じられることとなりました。
CFP宣言(開示)の義務化
まず最初に、対象となる電池(電気自動車用、一定容量超の産業用電池など)について、製造者は製品ごとのCFP値を算定し、第三者機関の検証を受けたCFP宣言書を作成する義務があります。この宣言書には、採用した算定方法、範囲、データ源、算出結果の値などが記載されます。CFP宣言の提出・登録は電池をEU市場に投入する前提条件となり、義務開始時期はEV用電池で2025年2月から、他の大型電池でも順次適用されます。宣言書の情報は後述のバッテリーパスポートにも格納され、規制当局が確認できるようになります。
CFP性能クラス分け
CFP値そのものを以って電池をランク付けする仕組みも導入予定です。具体的には、収集された各社のCFPデータをもとに、業界内での排出量水準を評価し、例えば「A~E」のようなクラス区分を設定します。これにより、自社の電池が市場平均に比べてどの程度低炭素かを示すことができます。性能クラスの表示は義務ではありませんが、将来的には製品カタログ等でアピール材料になる可能性があります。
CFP最大許容値の設定
規則で最も注目されるのは、一定期間後にCFPのしきい値(上限値)が導入される点です。
2025年~2026年頃に蓄積したCFPデータをもとに、欧州委員会が「この値以上のCFPを持つ電池は販売不可」とする基準値を策定・公表する予定です。その上限規制が施行されるのが2028年と見込まれており、それ以降は高排出な電池はEU市場に流通できなくなります。これは世界でも例のない革新的な規制で、各メーカーは自社のCFPをその上限以下に抑えることが生き残りの必須条件となります。
このように、欧州電池規則はCFPを「計測→公開→規制値設定」というステップで扱うことで、業界全体の脱炭素化を段階的に促しています。初期段階では透明性の確保(見える化)に重きを置き、その後データに基づき実効性ある基準を設定する手法は、かつての車の燃費規制などにも通じるアプローチです。企業にとってCFPへの対応は、単なる計算業務に留まりません。上限値規制が現実となれば、製造時のCO₂排出を低減するための投資(再生エネルギー利用、設備効率化)が避けられず、サプライヤーにも協力を仰ぐ必要が出てきます。また、CFP情報は環境ラベルや顧客への説明資料としても活用されることになるため、営業面でも自社電池のCFPを意識したPR戦略が求められます。
3. 欧州電池規則対応で企業が計測・報告すべきデータ
CFP算定・報告の実務対応において、企業が扱うべきデータは多岐にわたります。適切なCFP算定を行うには、ライフサイクルの各段階から次のような情報を収集しなければなりません。
原材料・部品の情報
電池に使用される材料(正極材、負極材、電解液、セパレーター、筐体など)ごとの原料採掘から精製までのCO₂排出係数が必要です。例えば1kgのリチウムを精製するのに何kgのCO₂が排出されるか、1kgのアルミニウムを生産するのに何kgのCO₂が出るか、といったデータです。これらはサプライヤーからの提供データや文献値、データベース(e.g., Ecoinvent)から取得します。主要材料についてはサプライヤーと直接やり取りし、できれば実測値や環境ラベル(EPDなど)の値を入手すると精度が上がります。
製造工程のエネルギー使用
自社(あるいは委託先)の電池セルおよびパック製造工場における電力・熱エネルギー消費量のデータが必要です。工場全体の年間エネルギー使用量を製品生産量で割って単位製品あたりのエネルギーを算出し、それに工場の電力原単位(電力会社のCO₂排出係数)を掛け合わせて製造由来のCO₂排出量を求めます。例えばセル1個あたりの製造に電力10kWh(電力CO₂係数0.5 kg-CO₂/kWh)使えば、それだけで5kg-CO₂がCFPに計上されます。クリーン電力を導入すればこの部分を削減できるため、エネルギーデータの把握は削減策検討にも役立ちます。
物流・輸送のデータ
原材料や部品を工場まで運ぶ際、および製品を市場まで配送する際の輸送起因排出も考慮します。輸送距離、手段(船舶、航空、トラック等)、重量から排出量を算出します。国際物流が絡む場合、海上輸送なら輸送1トンキロあたりのCO₂係数、航空輸送なら別途高い係数を適用します。電池は重量物なので、この輸送由来も無視できません。多くの場合、サプライチェーン上の輸送はLCAデータベースの標準値を使いますが、大量輸送を行っている企業は実データを用いると精度が上がります。
使用後・リサイクルのシナリオ
電池が廃棄された後、どのように処理されるかによっても環境負荷は変わります。埋立処分されればそのまま終端の排出になります。欧州電池規則では、少なくとも事業者が責任を負うべきリサイクル工程について、標準シナリオでの排出を織り込むことになるでしょう。つまり、回収率目標などを踏まえ「一定割合はリサイクルされ、その工程でこれだけCO₂が出るが、新規採掘をこれだけ削減できるのでネットでは…」と評価します。この部分は現時点で詳細未定な部分もありますが、電池リサイクル事業者から得られるデータ(例えば1トンの使用済み電池を処理する際のエネルギー消費)などを準備しておく必要があります。
その他情報
上記以外にも、CFP報告書には使用したLCAソフトウェア名、参照したデータベースのバージョン、除外した工程の有無、割り当てルールの考え方(副産物がある場合のCO₂配分)など技術的情報を記載する必要があります。これらは環境専門部署やLCAコンサルタントの支援を受けて整備することになります。
データ収集にはかなりの労力がかかりますが、欧州委員会はメーカーがCFP情報を提出するためのITプラットフォームを用意する予定です。それに沿って情報を入力し、第三者検証機関の承認を得た上で提出する流れになるでしょう。
4. CFP削減に向けた取り組み事例
企業各社は、CFPの算定結果を踏まえて自社の電池製品のカーボンフットプリント削減に向けた様々な取り組みを進めています。そのいくつかの事例を紹介します。
再生可能エネルギーの活用
欧州の新興電池メーカーであるノースボルト(Northvolt)は、自社工場で使用する電力を水力や風力などの再生可能エネルギーでまかない、製造段階のCO₂排出を極力抑えています。さらに、製造工程で排出される熱を回収・再利用するなどエネルギー効率を高める工夫も凝らしています。その結果、同社の電池セルのCFPは従来比で大幅に低減され、EVメーカーからも高い評価を受けています。
リサイクル素材の積極活用
パナソニックやサムスンSDIなど大手電池メーカーは、製造工程で出るスクラップ(金属加工くず)をすぐに再生処理して材料に戻す「内部リサイクル」を進めています。これにより、新規原料を削減し、結果として原材料調達由来のCFPを下げることができます。また、将来的には市中から回収した使用済み電池から抽出したリサイクル金属も原料に組み込む計画を発表しています。例えばパナソニックは2030年までにコバルト調達を全てリサイクル・再利用品で賄う目標を掲げ、パートナー企業と高度リサイクル技術の開発に取り組んでいます。
製品設計の工夫
一部企業は電池セルやパックの設計段階からCFP低減を狙っています。例えば、ある電池メーカーはニッケルやコバルトといった高環境負荷の材料使用量を減らすため、代替材料としてマンガンや鉄など比較的環境負荷の低い元素を増やした新しい電極化学を採用しました。これにより、性能を維持しつつCFPを10%以上削減できたと報告されています。また、テスラ社は4680型セルに代表される大型セル化で生産効率を上げ、セルあたりの工場エネルギー使用量を低減することでCFP削減に寄与するとしています。
サプライヤー支援
自社だけでなくバリューチェーン全体で排出削減する動きも見られます。自動車メーカーのBMWは、電池セルサプライヤーに対し再生エネ電力で製造することを条件に契約を結び、間接的に電池CFPの低減を図っています。また調達段階から低炭素素材を選ぶ取り組みも広がっています(例:炭素中和アルミニウムの調達など)。
これらの事例は、「見える化」したCFPを具体的な削減アクションにつなげている好例です。各社とも欧州電池規則を見据え、CFP削減が将来の競争力に直結すると判断して投資・施策を講じています。規則が本格施行されるこれから数年で、さらに多くのイノベーションが生まれることが期待されます。特にノースボルト社は、リサイクル素材100%で電池を製造するという画期的な実証にも成功しています。2021年、同社は使用済み電池から回収したニッケル・マンガン・コバルトのみを用いて、新品同等性能のリチウムイオン電池セルの製造に世界で初めて成功しました。これは資源採掘由来のCO₂排出を大幅に削減できる可能性を示す成果であり、同社は2030年までに自社生産電池の50%をリサイクル金属由来にする目標を掲げています。こうした先進事例は、CFP削減とサーキュラーエコノミー推進が両立可能であることを証明しており、規則遵守への取り組みに悩む企業にとって一つの指針となるでしょう。
引用元
ISO(国際標準化機構)公式サイト
欧州委員会:Product Environmental Footprint (PEF) Methodology
https://ec.europa.eu/environment/eussd/smgp/PEFCR_OEFSR_en.htm
Ecoinvent(LCAデータベース)
https://ecoinvent.org/
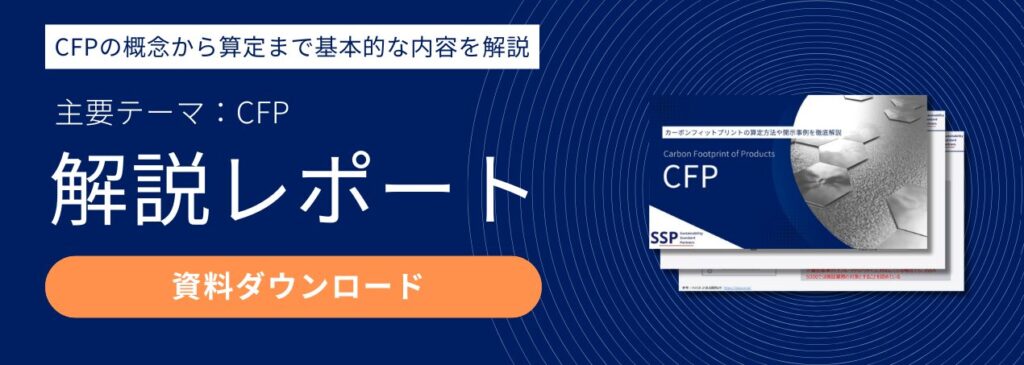
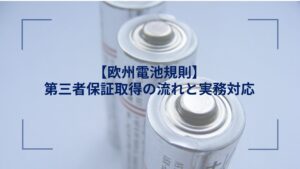