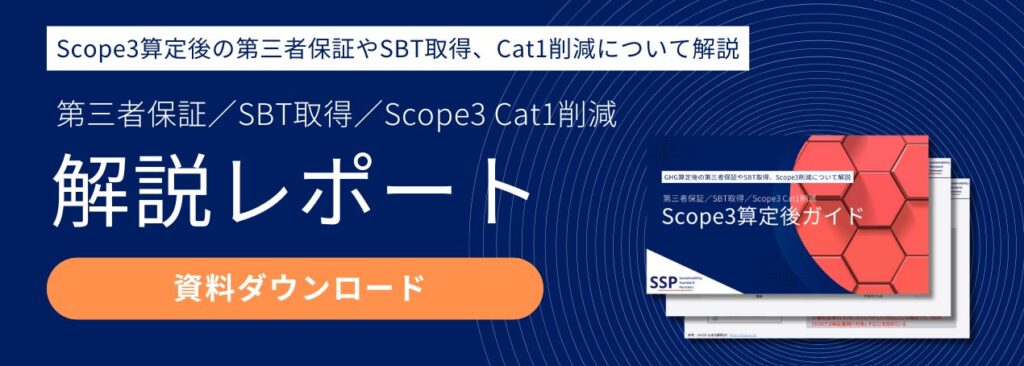
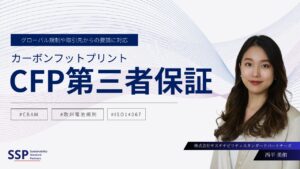
1.電子部品業界とカーボンフットプリントの重要性
半導体やプリント基板、コネクタ、センサーなどを製造する電子部品業界は、デジタル社会を支える中心的存在です。しかし高度な精密加工やクリーンルーム環境を維持するために多量の電力と処理ガスを消費し、原料の採掘・精製から製品使用後の廃棄に至るまで温室効果ガス排出が広範に発生します。国連の試算では ICT 機器関連の排出が世界全体の 3–4 % を占めるとされており、その大半は部材製造と使用段階のエネルギー消費に起因します。したがって電子部品メーカーが製品ごとのカーボンフットプリント(以下 CFP)を可視化し、ライフサイクル全体で削減策を講じることは、サプライチェーン全体の脱炭素推進に直結します。
Scope 1 と Scope 2 の排出構造
工場内で LNG や LPG を燃焼するドライオーブン、樹脂封止に用いる加熱設備、洗浄工程で用いる高温蒸気は Scope 1 の直接排出に該当します(電動や他社から購入している蒸気の場合はScope2)。また、電力と蒸気を大量に利用するクリーンルームやエッチング装置は Scope 2 の間接排出を押し上げる主因です。とりわけ先端半導体の製造ではプロセスガスとしてパーフルオロカーボン類(PFC)やハイドロフルオロカーボン類(HFC)が使われることが多く、温室効果係数が二酸化炭素の数千倍に達するため、わずかな漏えいでも排出量が一挙に増大します。
Scope 3 とライフサイクル全体の影響
電子部品の CFP を算定すると、部品製造以前の原材料調達および製造後の使用段階が総排出量の七割以上を占めるケースが一般的です。シリコンウエハー、銅配線、金やパラジウムなどの貴金属、エポキシ樹脂、ポリイミドフィルムといった材料は採掘・精錬・重化学加工を経ており、原単位当たりの排出係数が高い傾向があります。さらに、完成品が組み込まれる電子機器の使用期間中の電力消費は Scope 3 カテゴリ 11 に該当し、コンシューマ向け製品では製造排出を上回ることも珍しくありません。したがって電子部品メーカーは社内排出だけでなく、部材サプライヤーやセットメーカーと連携してライフサイクル全体を管理する必要があります。
2.CFP算定の技術的課題とデータ戦略
電子部品のサプライチェーンは多層構造で、 Tier2・Tier3 に鉱山会社や化学品メーカーが位置しており、一次データを遡及的に取得することが難しい場合が多々あります。製造委託(ファウンドリー)を活用するファブレス企業は、自社設備の稼働データを保有していない点も課題です。
多層サプライチェーンの可視化
近年は業界団体が PCF(Product Carbon Footprint)共有プラットフォームの整備を進め、共通フォーマットで排出係数を授受できる環境が整いつつあります。例えば IPC や JEITA が策定したデジタルバッジは、BOM(部品表)単位で原料重量と排出係数を登録できるため、セットメーカーは BOM を読み込むだけで製品全体のライフサイクル排出を試算できます。データがない場合は ecoinvent や IDEAv3 といった LCA データベースの代表値で補完しますが、代表値と実測値の乖離を継続的にモニタリングし、主要サプライヤーとは NDA を結んで一次データ精度を高めることが推奨されます。
部品使用段階の排出推計
電子部品自体はミリワットオーダーの電力しか消費しなくとも、完成機器では数十ワットから数百ワットの電力を長時間使用します。そのため CFP を算定する際は、想定される機器構成と平均使用年数、地域別電源構成に応じた排出係数を組み合わせる必要があります。特に EV 向けパワーモジュールやデータセンター向け FPGA など高負荷用途では、使用段階がライフサイクル排出のボトルネックになります。最近は IoT デバイスの低消費電力化を売りにする半導体メーカーが、LCA の結果を製品カタログに掲載し、省エネ効果を定量的に訴求する動きも見られます。
3.規制・市場動向と対応策
国際的には IFRS S2 が気候関連情報の開示を義務づける方向で動いており、電子機器を上流から下流まで提供する企業は Scope 3 の算定・報告を避けて通れなくなりました。米国証券取引委員会(SEC)の気候情報開示ルール案も同様の潮流を示しています。
投資家要求と国際開示基準
機関投資家は電子部品メーカーに対し、製品ポートフォリオ全体の排出強度(t-CO₂e/売上高)や省エネ性能の改善率を定量的に開示するよう求めています。サステナビリティ会計基準委員会(SASB)は電子機器・半導体セクターの重要項目として「エネルギー管理」「材料効率性」「製品寿命延長」を挙げており、CFP 算定はこれら指標の裏付けとなります。
欧州 CBAM と原材料リスク
欧州連合では 2026 年に炭素国境調整メカニズム(CBAM)が本格稼働し、鉄鋼やアルミに加え、将来的に銅・ニッケル・化学品も対象に含まれる可能性があります。電子部品はアルミ配線や銅リードフレームを多用するため、原材料の潜在的炭素コストがサプライチェーンに転嫁されるリスクがあります。メーカーは低炭素電炉鋼やリサイクルアルミの採用を検討し、原料段階から排出を抑える戦略が必要です。
4.低炭素化に向けた先進的取り組み
台湾の大手ファウンドリー T 社は太陽光発電と洋上風力を組み合わせた PPA 契約を締結し、2025 年までにグローバル拠点の 60 % を再生可能エネルギー由来に切り替える計画です。これにより Scope 2 排出を年間 300 万 t-CO₂e 超削減できると試算されています。日本の半導体メーカー N 社は化学気相成長(CVD)工程で発生する PFC ガスを、プラズマ分解装置で窒素と CO₂ に分解して排出係数を 90 % 以上削減しました。また欧州のコネクタメーカーは真鍮端子を再生銅 100 % に置き換え、製品あたりの原材料排出を半減させると同時に、サプライチェーンの価格変動リスクも緩和しています。
製造プロセスの電化と再エネ化
高温プロセスを電気ヒーターやマイクロ波加熱に置き換える動きも進んでいます。電化によってプロセス温度制御が精密になり歩留まりが向上する副次効果も報告されており、エネルギーコスト削減と品質改善を同時に実現できる点が評価されています。
サーキュラーエコノミーと材料転換
電子部品は小型で材料回収が難しいとされてきましたが、リーパー技術や選択的溶媒分離の進展により、高純度銅や貴金属を基板から分離・再利用するケースが実証段階に入っています。バイオベース樹脂や可食性基板など、従来と全く異なる素材を用いた環境配慮型デバイスの研究も盛んになっています。
5.まとめ
電子部品業界はデジタル社会の隠れた排出源として注目されつつあり、Scope 3 を含むライフサイクル排出の可視化と低減策の実装は、もはや競争優位の源泉です。多層サプライチェーンを俯瞰しながら高精度の CFP データを蓄積し、投資家や顧客に対して透明性の高い情報開示を行う企業ほど、調達先として選好される傾向が強まっています。今後はブロックチェーンやクラウド連携 LCA ツールの普及により、リアルタイムで製品別排出を更新し、設計段階で最適解を提示する「カーボンスマート設計」が主流になると予想されます。電子部品メーカーは自社工場の脱炭素と同時に、材料技術革新と循環型ビジネスモデルの構築を進めることで、気候変動時代におけるサステナブル・イノベーションの担い手として存在感を高めるでしょう。
引用
世界銀行レポート
https://documents.worldbank.org/en/publication/documents-reports/documentdetail/099121223165540890/p17859702a98880540a4b70d57876048abb?utm_source=chatgpt.com
世界経済フォーラム
https://www.weforum.org/stories/2024/05/data-growth-drives-ict-energy-innovation/?utm_source=chatgpt.com
Medium 解説
https://medium.com/%40jolindsaywalton/what-is-icts-global-carbon-footprint-1da8874ddc49