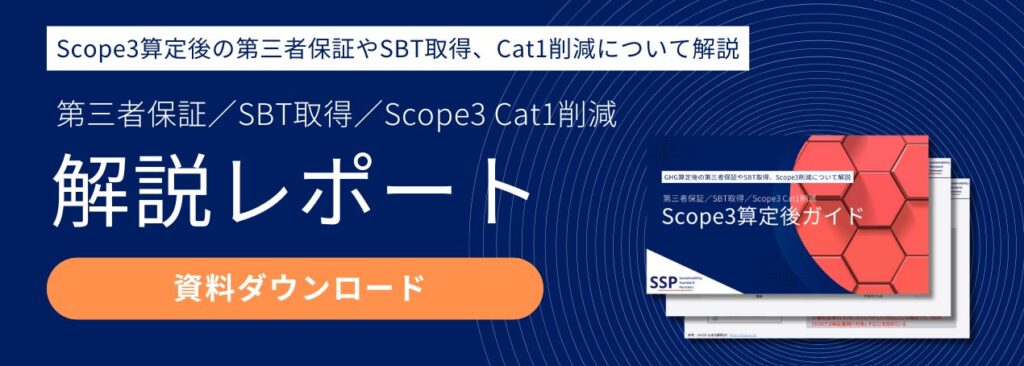
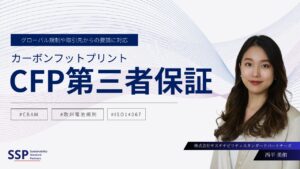
1.自動車産業が直面する脱炭素プレッシャー
自動車産業は製造業の裾野が広く、鉄鋼、アルミニウム、プラスチック、ガラス、ゴム、電子部品など多種多様な素材と部品を必要とします。完成車一台あたりの部品点数は三万点ともいわれ、その調達・加工・組立に伴う温室効果ガス(GHG)排出は膨大です。さらに、車両が道路を走り続ける使用段階では、燃料の燃焼による CO₂ 排出あるいは電動車の充電電力に起因する排出が長期にわたり発生します。
道路輸送部門はエネルギー起源 CO₂
国際エネルギー機関(IEA)の試算によれば、道路輸送部門はエネルギー起源 CO₂ 排出の約 15% を占め、そのうち乗用車だけで 45 億トンに達します。こうした状況を背景に、EU や英国、カリフォルニア州をはじめとする各国地域では 2030~40 年代にガソリン・ディーゼル新車販売を段階的に禁止する方針が相次いで表明されました。投資家も自動車メーカーに対し、ライフサイクル全体を通じた脱炭素戦略の開示を強く求めています。
2.自動車のライフサイクル排出構造
自動車のカーボンフットプリント(CFP)は、「材料製造・部品生産」「車両組立」「物流」「使用」「廃棄・リサイクル」という五つの主要段階で構成されます。ライフサイクル評価(LCA)に基づく実証研究では、内燃機関車(ICE)の場合、使用段階が総排出量の 70~80% を占める一方、バッテリー電気自動車(BEV)では走行時排出が電源構成に左右されるため、車両製造およびバッテリー生産の寄与率が 40% 近くに上昇するとの結果が報告されています。鉄鋼、アルミ、プラスチックといった主要材料だけで車両1台当たり平均 5~6 トンの CO₂e を排出し、これにバッテリーの正極材(ニッケル、コバルト、リチウム)や半導体部品の排出が上乗せされます。つまり、自動車メーカーの Scope1・2 排出は総量のわずか数%に過ぎず、Scope3、特にカテゴリ 1(購入した製品・サービス)とカテゴリ 11(販売した製品の使用)が圧倒的に支配的です。
3.CFP 算定の技術的ハードル
第一のハードルは多層サプライチェーンのデータギャップです。
サプライチェーン
Tier3 以降の部品供給網には中小企業が多く、ISO 14067 や GHG プロトコル製品基準に対応した排出データを保有していないケースが目立ちます。 OEM が統合プラットフォームを通じて部品表(BOM)単位の排出係数を収集する動きは加速していますが、材質や工程ごとのバリエーションを考慮すると代表値との乖離が大きくなりがちです。
車両使用段階のシナリオ設定
第二のハードルは車両使用段階のシナリオ設定です。地域別の平均走行距離、燃費、エネルギーミックスをどう想定するかによって結果が大きく変動します。例えば同一 BEV でも、ノルウェーの電源構成(再エネ比率 90% 超)で算定した使用排出は、中国の石炭依存度が高い地域での算定値の 5 分の 1 程度まで低減します。
副生成物の割当
第三のハードルは副生成物の割当とリサイクルクレジットです。鉄鉱石から鉄を製造する際に発生する副産ガスのエネルギー回収や、使用済み車両の金属リサイクルによる排出削減効果をどこまで差し引くかは、算定者のアサンプションに依存します。よって、計算条件の透明性を確保し、国際標準と齟齬がないかを検証するプロセスが欠かせません。
4.国際規格とガイドラインの整合
自動車 CFP を算定する際は、ISO 14040/44 による LCA の一般原則を踏まえつつ、ISO 14067 が示す製品 CFP の要求事項を満たす必要があります。
EU
EU では Product Environmental Footprint Category Rules(PEFCR)の自動車版が策定中で、今後は EU 市場で販売される車両の環境性能比較に活用される見通しです。業界団体では欧州自動車工業会(ACEA)が「CO₂ life cycle assessment guidelines」を発行し、OEM 各社が共通フォーマットで排出データを公表する仕組みを整えました。さらに、独 BMW、メルセデス・ベンツ、フォルクスワーゲングループなどが参加する Catena-X コンソーシアムは、ブロックチェーンを活用した部品単位の PCF 共有システムを開発し、2024 年から本格運用を開始しています。日本でも自工会・部工会が連携し、部品共通データフォーマットの標準化を進めており、Tier2 以降を巻き込んだ排出係数の横断的収集体制が構築されつつあります。
5.材料転換と製造プロセスの低炭素化
鉄鋼は車体重量の約六割を占める最大排出源ですが、高炉から電炉へのシフトや水素還元製鉄(H₂ DRI)の商用化により、製造段階の排出を 90% 以上削減できる可能性が示されています。アルミニウムについても、再生アルミの投入比率を 60% から 90% に高めるだけで車両当たり数百キログラムの CO₂e 削減が見込めます。プラスチック部品では植物由来のバイオ PP やリサイクル材のクローズドループ利用が拡大しつつあります。また、車両組立工場では電化塗装ブースやオンサイト太陽光発電による再エネ化が進み、ドイツの大手メーカーは 2030 年までに組立工場の Scope2 排出実質ゼロを宣言しました。こうした個社努力に加え、2026 年に本格施行される EU CBAM では鉄鋼やアルミの輸入時に暗黙の炭素税が課されるため、上流材料の低炭素化は OEM にとって必須条件となりつつあります。
6.バッテリー電気自動車の算定論点
BEV の CFP を議論する際に避けて通れないのがバッテリー製造の影響です。リチウムイオン電池パック 1 kWh あたり 60~100 kg-CO₂e の排出が報告されており、60 kWh クラスのバッテリーを搭載する Cセグメント車では 4~6 トンの製造排出が追加されます。ただし再エネ電力を導入した最新ギガファクトリーでは排出原単位が半減した例もあり、正極材のコバルトフリー化やリサイクル資源投入率の上昇によってさらに低減が期待されます。EU バッテリー規則(Battery Regulation)は 2025 年以降、BEV バッテリーに対して製造段階のカーボンフットプリント開示を義務付けるとともに、2030 年には一定値以下でなければ販売できない門番制度(しきい値制度)を導入予定です。自動車メーカーはバッテリーサプライヤーと協働し、原料採掘からセル製造までの排出データを統合管理する MRV 体制を確立することが急務です。
7.使用段階と電源ミックス
車両使用フェーズの排出は、燃料・電力のライフサイクル排出係数と走行距離で決まります。ICE ではTank to Wheel(燃焼)排出のほか、ウェル・トゥ・タンク(燃料製造・輸送)排出も計上する必要があります。一方 BEV の場合、国別電源ミックスが排出量を大きく左右します。太陽光や風力の比率が高い北欧では走行 1 km あたり 20 g-CO₂e 前後まで低減できるのに対し、石炭依存の高い地域では 100 g-CO₂e を超える場合もあります。再エネの追加性を担保した PPA や充電インフラの V2G(Vehicle to Grid)活用が進めば、将来的に BEV の使用段階排出を実質ゼロ近くまで抑制できる見通しです。
8.廃車・リサイクルと循環型モデル
ELV(End-of-Life Vehicle)指令改正案では、2035 年以降に EU で登録される新車のプラスチック部品に最低 25% の再生材使用を義務付け、うち 25% は車両由来であることを求める方針が示されています。日本でも自動車リサイクル法の改正検討が始まり、バンパーからバンパーへリサイクルする水平リサイクルの実証が進んでいます。車両の LCA においては、再資源化率の向上に伴うリサイクルクレジットをどの段階で控除するかが論点になりますが、国際的には「将来便益は保守的に見積もる」原則が浸透しつつあり、車両 CFP の算定式においてもリサイクル材使用率を実効的に反映する枠組みが採用されつつあります。
9.算定プロセスと検証フロー
自動車 CFP を算定する際の一般的な流れは、目的・範囲の設定、ライフサイクルインベントリ(LCI)データ収集、インパクト評価、結果統合と解釈、報告・検証の五段階です。目的設定では、車種やパワートレイン別に機能単位(1 台、1 km 走行など)を決め、システム境界を「ウォール・トゥ・ホイール」あるいは「クレードル・トゥ・グレイブ」で定義します。LCI では BOM、工程別エネルギー、物流距離、バッテリー構成などを詳細に入力し、GaBi、自動車専用 LCA ツール(Sphera Automotive Suite など)を用いて排出量を算定します。報告フェーズでは前提条件と不確実性を明記し、第三者検証(ISO 14064-3 や PAS 2050)を受審することで外部ステークホルダーの信頼を確保します。 Catena-X や JAMA のデジタルプラットフォームを活用して部品ベースの排出情報を自動連携すれば、検証作業の効率を高めることが可能です。
10.今後の展望と経営インパクト
ICE のフェーズアウトと BEV への急速な移行は、自動車業界の CFP プロファイルを劇的に変化させます。車両製造段階、特にバッテリー・鉄鋼・アルミの排出が競争力の決定要素となり、低炭素材料の確保と原料価格リスクマネジメントが不可欠です。さらに、使用段階での再エネ充電インフラ整備や V2G 活用が、新たなビジネスモデル創出の起点になります。ステークホルダーはデータに基づく科学的アプローチを重視しており、OEM とサプライヤーは共通基盤で CFP データを共有し、製品設計フェーズから排出削減シナリオを組み込む「カーボン・イン・デザイン」の実装が求められます。CFP 算定は単なる報告義務ではなく、サプライチェーン全体の競争優位を左右する経営戦略であることを、いま一度認識する必要があるでしょう。
引用
ACEA(欧州自動車工業会)
https://www.acea.auto/files/ACEA_position_paper-Life_Cycle_Assessment.pdf?utm_source=chatgpt.com
EU規則 2023/1542 Batteries and Waste Batteries Regulation
https://eur-lex.europa.eu/eli/reg/2023/1542/oj/eng?utm_source=chatgpt.com
EU規則 2023/956 Carbon Border Adjustment Mechanism
https://eur-lex.europa.eu/eli/reg/2023/956/oj/eng?utm_source=chatgpt.com